ทฤษฏีข้อจำกัด (Theory of Constraints : TOC) ถูกพัฒนาขึ้นโดย Goldratt หลักการสำคัญของ TOC คือ ทุก ๆ ระบบเปรียบเหมือนห่วงโซ่ที่ร้อยเรียงกัน ในแต่ละห่วงโซ่จะประกอบด้วยจุดเชื่อมต่อที่มีความสามารถแตกต่างกันไป จะมีห่วงโซ่อยู่ห่วงหนึ่งที่อ่อนแอที่สุด เรียกว่า Weakest Link Weakest Link จะเป็นข้อจำกัด (Constraint) ของความสามารถทั้งระบบ เปรียบไป
Tag: วิทยากร LEAN
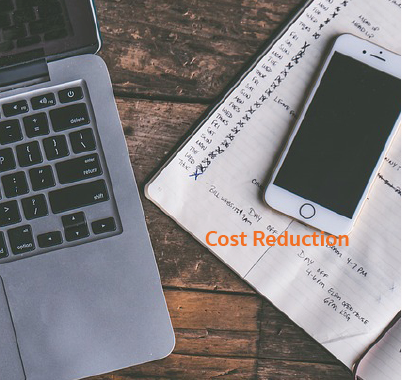
ในช่วงภาวะเศรษฐกิจฝืดเคืองเช่นนี้ บริษัทต่าง ๆ จำเป็นอย่างยิ่งที่ต้องหากลยุทธ์หลากหลายเข้ามาบริหารจัดการ เพื่อนำพาองค์กรให้ฝ่าวิกฤติเศรษฐกิจไปให้ได้ ซึ่งสามารถทำได้ 2 รูปแบบใหญ่ ๆ คือ กลยุทธ์ฝ่าด่านภายนอก คือ การใช้กลยุทธ์ทางการตลาดเป็นตัวนำที่จะสร้างความแตกต่างจากคู่แข่งขัน เพื่อให้ได้มาซึ่งส่วนแบ่งการตลาดที่เพิ่มขึ้น ราคาขายที่เพิ่มขึ้น กลยุทธ์รีดไขมันภายใน คือ การนำระบบการบริหารงานแบบลีน (Lean Management) เข้ามาช่วยจัดการการทำงานให้มีประสิทธิภาพ ลดการสูญเสียในกระบวนการต่าง ๆ เพื่อทำให้ต้นทุนลดต่ำลง ก็จะส่วนแบ่งกำไรที่เพิ่มขึ้น
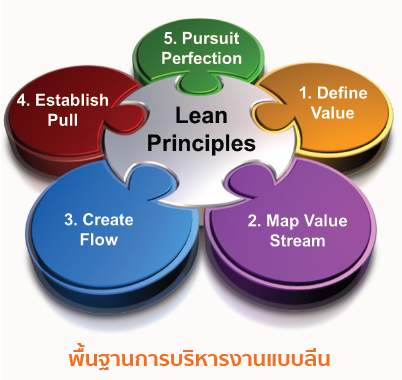
ในการบริหารงานแบบลีน (Lean Management) นั้นมีพื้นฐานหลักอยู่ด้วยกัน 5 ประการ คือ Define Value – กำหนดคุณค่าของสินค้า จากมุมมองของลูกค้า ทั้งภายในและภายนอก Map Value Stream – การสร้างแผนผังสายธารคุณค่าในปัจจุบัน และอนาคตในสิ่งที่อยากเห็น หาทางขจัดความสูญเปล่าที่เกิดขึ้นในปัจจุบัน Create Flow – สร้างให้เกิดการไหลของงานอย่างต่อเนื่อง ขจัดอุปสรรคต่าง
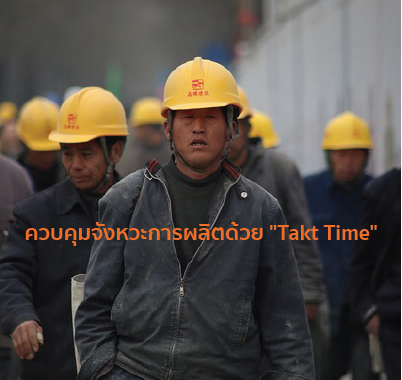
ค่า “Takt Time” คือ จังหวะความต้องการสินค้าของลูกค้า Takt เป็นภาษาเยอรมันที่ใช้เรียกจังหวะของเครื่องดนตรี ดังนั้น Takt Time คือ อัตราการผลิตที่ต้องผลิตเพื่อให้สอดคล้องกับปริมาณความต้องการของลูกค้า การคำนวณหาค่า Take Time = Available Time / Demand ตัวอย่างเช่น โรงงานแห่งหนึ่งมีความต้องการสินค้า (Demand) อยู่ที่ 420
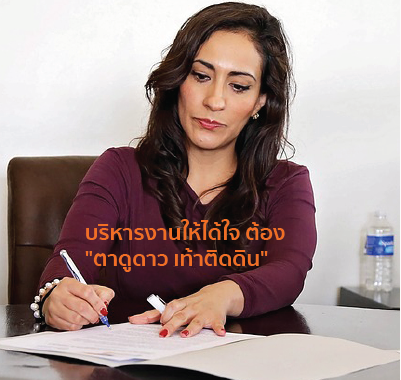
คนที่เป็นหัวหน้างาน ผู้จัดการ ผู้บริหารในองค์กร มักจะโดนผู้ใต้บังคับบัญชาค่อนแคะอยู่เสมอว่า ทำตัวเหินห่าง ไม่ค่อยรู้เรื่อง หรือสนใจงานประจำวันสักเท่าไหร่ ชอบทำตัวอยู่บนหอคอยงาช้าง ดังนั้นการที่จะบริหารงานให้ได้ใจลูกน้องนั้นต้อง “ตาดูดาว เท้าติดดิน” ซึ่งในหลักการบริหารเรียกวิธีการทำงานสไตล์ถึงลูกถึงคนแบบนี้ว่า Management by Walking Around ซึ่งนอกจากจะได้ใจลูกน้องแล้ว ก็ยังได้ลงไปรับรู้ปัญหาที่เกิดขึ้นจริง สามารถแก้ไขปัญหาได้อย่างทันท่วงที มีโอกาสสื่อสารโดยตรงกับคนทำงาน ซึ่งการนำแนวการบริหาร Management by Walking Around
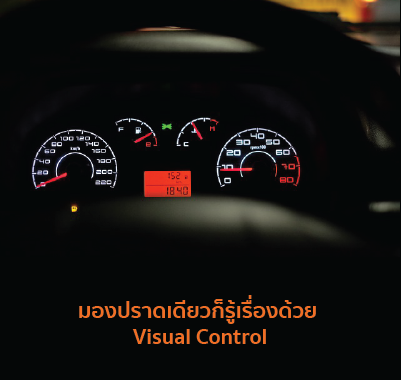
“สิบปากว่า ไม่เท่าตาเห็น” เป็นสิ่งที่บ่งบอกให้เห็นถึงความสำคัญของระบบการควบคุมด้วยการมองเห็น (Visual Control) Visual Control คือ วิธีการบริหารงานที่มองปราดเดียวก็รู้ว่า เกิดความผิดปกติขึ้นหรือไม่ รวมทั้งช่วยสื่อสารให้ชัดเจนขึ้น เพื่อนำไปสู่การปฏิบัติงานที่ถูกต้อง Visual Control ที่ใกล้ตัวเรามาก ๆ ก็คือ หน้าปัดรถยนต์ ที่ทำหน้าที่บอกระดับน้ำมัน ความร้อนของหม้อน้ำ ความเร็วของรถ รอบของเครื่องยนต์ เป็นต้น ดูรายละเอียดหลักสูตร “Business
ในหลักการบริหารจัดการแบบลีน (Lean Management) นั้น ต้องออกแบบกระบวนการให้มีการไหลลื่นไม่ติดขัด Flow อย่างต่อเนื่อง แต่แล้วสิ่งที่เกิดขึ้นในกระบวนการทำงานนั้น ล้วนแต่มีสิ่งที่เป็นอุปสรรคต่อการไหลลื่น อันประกอบไปด้วย 3 MU ได้แก่ Muda – ความสูญเสียที่เกิดขึ้นในงาน อันประกอบไปด้วย “ความสูญเสีย 7 ประการ” Overproduction (การผลิตที่มากเกินไป) Inventory (การมีสินค้าคงคลังเกินความจำเป็น) Motion
“Jidoka” หมายถึง การควบคุมตัวเองโดยอัตโนมัติ เพื่อป้องกันการเกิด Defect ของชิ้นงานที่จะหลุดไปยังกระบวนการต่อไป คือ แทนที่จะปล่อยให้ไปตรวจพบของเสีย (Defect) ที่ปลายทางจำนวนมา ก็ให้รีบทำการหยุด Line การผลิตเพื่อแก้ไขทันที โดยมีเป้าหมายร่วมกัน คือ Zero Defect แนวคิดพื้นฐาน คือ จะต้องไม่ส่งของเสีย (Defect) ไปยังหน่วยงานถัดไป และป้องกันความเสี่ยงที่ของเสียจะหลุดไปถึงมือลูกค้าด้วย ดูรายละเอียดหลักสูตร “Business
Just-in-time : JIT คือ สถานะในอุดมคติที่มีการไหลของงานอย่างต่อเนื่อง (Continuous Flow) ที่เป็นไปตามความต้องการของลูกค้า ได้แก่ ทำเฉพาะสินค้าที่ลูกค้าสั่งเท่านั้น ทำให้เสร็จภายในเวลาที่ลูกค้าต้องการเท่านั้น ทำในปริมาณที่ลูกค้าต้องการเท่านั้น เพราะฉะนั้นการออกแบบกระบวนการไหลของสินค้า ตั้งแต่ขั้นตอนเตรียมวัตถุดิบ ไปผ่านขั้นตอนการแปรรูปต่าง ๆ จนกลายเป็นผลิตภัณฑ์ จนไปถึงกระบวนการบรรจุหีบห่อ และส่งมอบสินค้า จะต้องมีจังหวะที่สอดประสานกัน เกิดการไหลอย่างต่อเนื่อง ไม่มีจุดคอขวด (Bottleneck) ที่ทำให้กระบวนการชะงักงัน สภาวะในอุดมคติของ
เพราะทุกวินาทีมีค่า การทำงานที่ล่าช้าแม้เพียงเสี้ยววินาที อาจหมายถึง ความพ่ายแพ้ในการแข่งขัน SMED (Single Minute Exchange of Die) คือ เทคนิคในการลดเวลาการปรับตั้งเครื่องจักรให้อยู่ในระยะเวลาอันสั้นที่สุด โดยมีเป้าหมายต้องให้ไม่เกิน 10 นาที แต่ยิ่งรวดเร็วมากที่สุดเท่าไหร่ยิ่งดี ถูกคิดค้นขึ้น โดย Dr. Shingeo Shingo ซึ่งเป็นผู้ร่วมกันคิดระบบการผลิตแบบ โตโยต้า ร่วมกับ Taiichi Ohno