เมื่อเอ่ยถึง Learning Organization หลายคนจะนึกถึงหนังสือที่ชื่อว่า “The Fifth Discipline” ของ Peter M. Senge ซึ่งพูดถึงวินัยทั้ง 5 ประการ ขององค์กรแห่งการเรียนรู้ ได้แก่ Personal Mastery Mental Models Shared Vision Team Learning Systems
เพราะทุกวินาทีมีค่า การทำงานที่ล่าช้าแม้เพียงเสี้ยววินาที อาจหมายถึง ความพ่ายแพ้ในการแข่งขัน SMED (Single Minute Exchange of Die) คือ เทคนิคในการลดเวลาการปรับตั้งเครื่องจักรให้อยู่ในระยะเวลาอันสั้นที่สุด โดยมีเป้าหมายต้องให้ไม่เกิน 10 นาที แต่ยิ่งรวดเร็วมากที่สุดเท่าไหร่ยิ่งดี ถูกคิดค้นขึ้น โดย Dr. Shingeo Shingo ซึ่งเป็นผู้ร่วมกันคิดระบบการผลิตแบบ โตโยต้า ร่วมกับ Taiichi Ohno
ในวันนี้ (16/01/58) ได้มีโอกาสมาทำงานร่วมกับทีมงานของอาจารย์ไชยยศ ปั้นสกุลไชย เพื่อมาจัดฝึกอบรมในเรื่อง “Team Productivity” ให้กับบริษัทแห่งหนึ่ง ที่สวนสามพราน จ.นครปฐม ผมได้รับมอบหมายให้เป็นวิทยากรในช่วงหลังเบรคบ่าย ในการบรรยายหัวข้อ Kaizen เพื่อการปรับปรุงงานให้กับผู้เข้าอบรม และให้ผู้เรียนนำความรู้ที่ได้มาทำ Workshop ในการปรับปรุงงานของจริง ซึ่งหลังจากการฝึกอบรมอาจารย์ไชยยศ ก็ชวนทีมมานั่งล้อมวงคุยกันเพื่อทบทวนสิ่งที่เกิดขึ้นในการฝึกอบรมในวันนี้ เพื่อนำไปแก้ไขปรับปรุงให้ดียิ่งขึ้น ในภาษาทางการทหาร เรียกว่า AAR ที่ย่อมาจากคำว่า After
ระบบการบริหารงานหลายอย่างไม่ว่าจะเป็น 5S, TQM, TPM, TPS (Toyota Production System) หรือที่เรารู้จักกันในนามว่า “LEAN” นั้น มักมีคำถากถางคนไทยอยู่เสมอว่า “ระบบพวกนี้โตที่ญี่ปุ่น แต่ต้องมาตายที่เมืองไทย” ก็น่าสนใจนะครับว่าทำไมจึงเป็นเช่นนั้น ? ผมเองได้มีโอกาสไปศึกษาเรื่อง LEAN Production ที่ประเทศญี่ปุ่น เมื่อ 6 ปีที่แล้ว ช่วงที่เกิดเหตุการณ์ Tsunami
Affinity Diagram คือ เครื่องมือตัวหนึ่งที่จะช่วยจัดระเบียบความคิด จากการระดมสมอง เพื่อจัดไอเดียที่หลากหลายจำนวนมากมาย ออกเป็นกลุ่ม ๆ ที่มีความสัมพันธ์ใกล้เคียงกัน เพื่อนำไปสู่การหาข้อสรุปร่วมกัน โดยมีขั้นตอนดังนี้ ร่วมกันระดมสมอง เขียนไอเดียเป็นข้อความที่กระชับ 1 ไอเดียต่อ 1 แผ่น ลงบน Post-it และติดไว้บนกระดาน หรือผนังกำแพง เพื่อที่ทุกคนจะได้เห็นได้ทั่ว ช่วยกันย้ายไอเดียที่ดูจะสัมพันธ์กันไปไว้อยู่กลุ่มเดียวกัน หากไอเดียไหนไม่เข้าพวกก็แยกไว้โดด ๆ
เหตุใดที่ปัญหาที่เกิดขึ้น ไม่ว่าจะเป็นความผิดพลาดในงาน เครื่องจักร Breakdown จึงเกิดขึ้นบ่อยครั้ง แก้ปัญหาเท่าไหร่ก็ไม่เคยหายขาดซักที ลองถามตัวคุณเองดูว่า คุณยังวิเคราะห์ปัญหาแบบนี้อยู่หรือไม่ จู่โจมเข้าวิเคราะห์ปัญหาเลย ทั้งที่ยังไม่ได้รวบรวมข้อมูลข้อเท็จจริงให้ครบถ้วน เริ่มวิเคราะห์ทั้งที่ยังไม่เข้าใจสถานการณ์อย่างถูกต้อง เริ่มวิเคราะห์ทั้งที่ยังไม่ได้ไล่เรียงปรากฎการณ์ที่เกิดขึ้น เริ่มวิเคราะห์ทั้งที่ยังไม่เฟ้นหาปรากฎการณ์ที่ควรนำเจาะหาสาเหตุ วิเคราะห์ไปเรื่อย ทั้งที่ไม่ใช่การเจาะหาสาเหตุอย่างมีเหตุมีผล ยุติการวิเคราะห์ ทั้งที่ยังไม่พบสาเหตุที่แท้จริงของปัญหา หากคุณยังมีอาการในการวิเคราะห์ปัญหาเช่นนี้ การแก้ปัญหาก็จะเป็นการแก้ปัญหาแบบชั่วคราวเพื่อบรรเทาอาการของปัญหาเท่านั้น แต่ยังไม่ได้เข้าไปแก้ปัญหาที่แท้จริงของปัญหา Why-Why Analysis คือ เทคนิคในการวิเคราะห์สาเหตุที่แท้จริงของปัญหา ที่ไม่ได้แค่เป็นการนึกคิดหาสาเหตุของปรากฎการณ์ที่ทำให้เกิดปัญหาหนึ่ง
กุญแจสำคัญในการบริหารงานแบบลีน (Lean Management) ประกอบไปด้วย การทำให้ลูกค้าพึงพอใจ คือ ให้บริการได้อย่างมีคุณภาพมากขึ้น ภายใต้เวลาที่น้อยลง รวดเร็วขึ้น การมุ่งเข้าไปปรับปรุงกระบวนการ โดยเข้าไปขจัดข้อบกพร่อง (Defect) ที่ลูกค้าไม่ต้องการออกไป การร่วมกันทำงานเป็นทีม ที่จะช่วยกันแบ่งปันความคิดในการร่วมกันแก้ปัญหา การอ้างอิงข้อมูลข้อเท็จจริง (Fact Based) ในการตัดสินใจ โดยจุดเริ่มต้นต้องเริ่มจากข้อแรก คือ การทำให้ลูกค้าพึงพอใจ ที่จะต้องไปสืบค้นถึงความต้องการที่แท้จริงของลูกค้า ฟังเสียงของลูกค้า (Voice
เพื่อให้การปรับปรุงกระบวนการโดยการนำแนวคิดบริหารแบบลีน (Lean Management) มาใช้ สามารถวัดและประเมินมูลค่าความสูญเสียที่เกิดขึ้นที่สามารถเชื่อมโยงสะท้อนไปที่บัญชีต้นทุนได้อย่างแท้จริงว่า สามารถลดต้นทุนจากการลดความสูญเสียในกระบวนการได้เท่าไหร่ ก็จะต้องนำแนวคิดของ “MFCA” มาประยุกต์ใช้ “MFCA” คือ อะไร ? MFCA ย่อมาจากคำว่า Material Flow Cost Accounting บัญชีต้นทุนการไหลวัสดุ ที่มีจุดเริ่มต้นจากประเทศเยอรมนี และมาเริ่มใช้แพร่หลายในประเทศญี่ปุ่นในช่วง 10 กว่าปีที่ผ่านมา โดยมุ่งเน้นที่จะเข้าไปวัดมูลค่าวัตถุดิบ
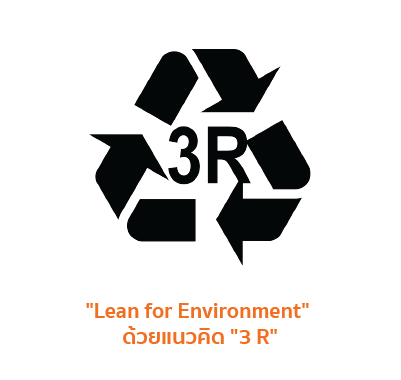
การปรับปรุงงานด้วยการนำแนวคิดการบริหารงานแบบลีน (Lean Management) มาใช้นั้น นอกจากเพื่อวัตถุประสงค์ในการทำให้งานคล่องตัวแล้ว ก็ยังมีวัตถุประสงค์ในด้านสิ่งแวดล้อมด้วยเช่นกัน เรียกว่า “Lean for Environment” โดยนำแนวคิด “3 R” มาประยุกต์ใช้ อันได้แก่ R – Reduce การลดการใช้ทรัพยากรต่าง ๆ ไม่ว่าจะเป็นวัตถุดิบ พลังงานไฟฟ้า น้ำ เชื้อเพลิง โดยพยายามเข้าไปลดจุดรั่วไหลที่เกิดขึ้นในกระบวนการ
การนำระบบการบริหารงานแบบลีน (Lean Management) มาปรับใช้ ก็เพื่อมุ่งเน้นขจัดความสูญเสียให้หมดไป ความคาดหวังในทางอุดมคติ เรียกว่า ต้องพยายามอย่างเต็มที่ที่จะต้องทำให้เกิดขึ้น คือ การมุ่งสู่ “5 Zero” อันประกอบด้วย 1. ของเสียเป็นศูนย์ (Zero Defect) เนื่องจากของเสีย เป็นต้นทุน 2. การรอคอยเป็นศูนย์ (Zero Delay) เนื่องจากการรอคอยทำให้ใช้ประโยชน์จากทรัพยากรที่มีอยู่ เช่น